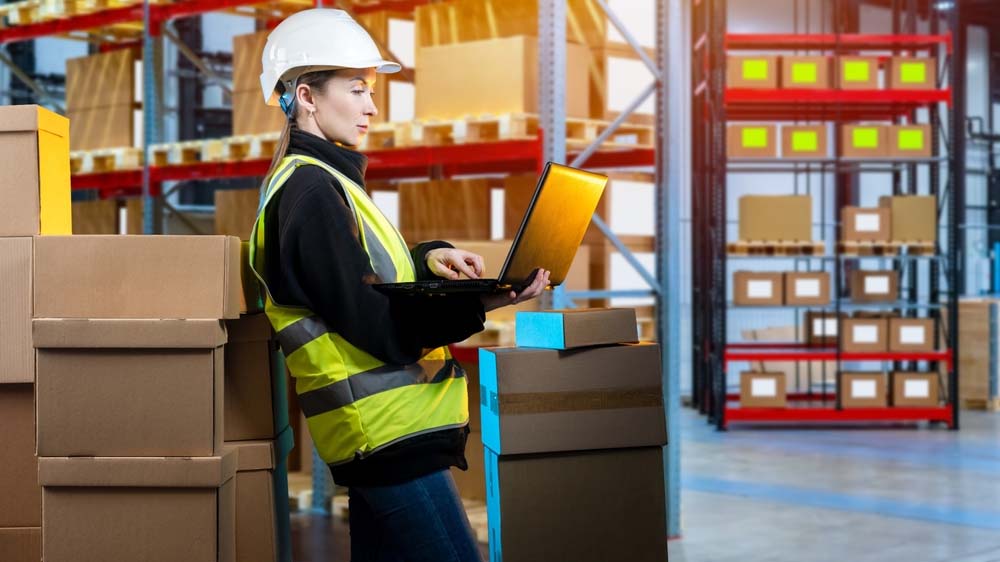
Inventory verification is the process of verifying the accuracy of a company's
inventory records, which are used to track the quantity, value, and location of the
goods and materials that a business has on hand.
This process is important because it helps businesses ensure that their inventory
records are accurate and up-to-date, which is essential for accurate financial
reporting and effective inventory management.
Any type of verification requires a lot of time and manual work, but it offers a
thorough analysis of a company’s various accounts and their financial status.
Let us start understanding the procedure of Physical Inventory Verification.
Procedure
Here are the key steps involved in inventory verification :
● Identify the inventory to be verified
The first step in inventory verification is to identify the inventory that needs to be verified. This typically includes all goods and materials that are held in stock, such as raw materials, finished goods, and spare parts.
● Conduct a physical count of the inventory
The next step is to conduct a physical count of the inventory to verify its quantity and value. This typically involves physically counting each item of inventory and recording its details, such as its description, quantity, and value
● Verify the accuracy of the inventory records
Once the physical count is complete, the next step is to verify the accuracy of the inventory records. This involves comparing the physical count with the inventory records to ensure that they are accurate and up-to-date.
● Make any necessary adjustments to the inventory records
If any discrepancies are found during the verification process, the next step is to make any necessary adjustments to the inventory records. This may involve updating the quantity, value, or location of the inventory to reflect the results of the physical count.
● Prepare a report
Once the verification process is complete, the next step is to prepare a report that
summarises the results of the verification. This report should include any discrepancies
that were found and the actions taken to correct them.
Overall, inventory verification is an important process that helps businesses ensure the
accuracy and integrity of their inventory records. By conducting regular inventory
verifications, businesses can improve their financial reporting and inventory management,
and ensure that their inventory is properly accounted for
● Make any necessary adjustments to the inventory records
If any discrepancies are found during the verification process, the next step is to make any necessary adjustments to the inventory records. This may involve updating the quantity, value, or location of the inventory to reflect the results of the physical count.
Challenges
● Long and Time-consuming
The verification of physical inventory is a very long procedure. Because a company has several assets, the fixed asset verification procedure is typically drawn out and stressful. In addition, because some of the assets are in different places, validating each one of them might be a challenging procedure. Additionally, each paper is examined and corrected.
● Difficult to scale
As your company expands, you'll need to be more strategic about your inventory
solutions.In between complete physical inventory verifications, spot checking may
be a more practical approach to keep inventory audits under control. This entails
selecting a particular product, calculating the quantity on hand, and contrasting it
with the quantity recorded in the system.
By requiring a spot check when the system declares the product stock as zero to
assure there are no more units on hand, inventory management technology may
contribute to the simplification of inventory processes.
● Can halt operations
Operations, such as filling orders and shipping goods to clients, are halted if everything is put on hold to conduct an inventory verification. In the era of Amazon, satisfying consumer demands for prompt delivery might affect how they interact with your offering and form an opinion of your company.
Solutions
● Demand Forecasting
Understanding current counts is aided by inventory verification, but using data to guide future business choices is a very different matter. By analysing previous data, demand forecasting makes predictions about upcoming orders. This helps a corporation satisfy consumer expectations while making smarter decisions about inventory planning, product storage, and marketing campaigns.
● Preventive Control
To handle problematic inventory, such as perishable goods, delicate machinery, or outdated supplies, implement stock control systems. If the manufacturer specifies it, do routine preventative maintenance on the machinery and equipment stock that is kept in storage. To track shelf life and reduce waste, catalogue data on issue stock location, cost, and amount is available.
● Can halt operations
Operations, such as filling orders and shipping goods to clients, are halted if everything is put on hold to conduct an inventory verification. In the era of Amazon, satisfying consumer demands for prompt delivery might affect how they interact with your offering and form an opinion of your company.
● Preventive Control
You may examine the state of your inventory and choose whether to pro-actively refill inventory using software like PRF's. PRF Management Consultancy can project when you should send extra merchandise to prevent stockouts using the order history for your shop; there is no need to perform manual reorder point calculations again.
● Conclusion
Overall, inventory verification is an important process that helps businesses ensure
the accuracy and integrity of their inventory records. By conducting regular
inventory verifications, businesses can improve their financial reporting and
inventory management, and ensure that their inventory is properly accounted for.
We at PRF will provide business IT-enabled tools for effective and accurate
inventory management, assisting organisations in performing efficient and
frequent inventory audits, and controlling the inventory cycle end to end.
We cater to a wide range of management consultancy services in Dubai, providing
clients benefit of multi-disciplinary expertise under one single roof